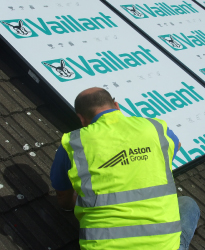
Renewable Energy
Our brief was to install a high efficiency solar hot water system within a void dwelling. The dwelling at the time of installation was under major refurbishment, being converted back from a number of bed-sit type units to one large house, giving 5 double bedrooms. The new solar system was to be linked to a... View Artic...
Click to read more
Our brief was to install a high efficiency solar hot water system within a void dwelling.
The dwelling at the time of installation was under major refurbishment, being converted back from a number of bed-sit type units to one large house, giving 5 double bedrooms.
The new solar system was to be linked to a new boiler / heating system which had recently been installed. The system was designed to give the maximum return by way of reduced cost hot water to the end user.
Procurement
Works was secured after competitive quotations had been submitted by a number of contractors, all the contractors who were invited to summit costs were chosen due to their ongoing working relationship with Waltham Forest Housing.
Our quotation was accepted not only for best valve but also for our detailed design proposals.
Equipment
Vaillant Ltd were the chosen manufacturer due to the new heating boiler being supplied by the same company they also have a range of Solar un-vented hot water cylinders, thus keeping the whole project with one main manufacturer. This will help with any future maintenance.
Supply chain
All equipment was supplied from local merchants, reducing the impact on the environment due to transportation. This also helps to support local business and their employees.
System Benefits
- Environment ~ Using solar energy, you are reducing the impact on the environment as a whole, the estimated carbon reduction could be as much as 325Kg / per year.
- The reduced use of standard methods of heating your hot water, helps to conserve the rapidly diminishing supplies of gas and oil, thus helping to curb the every rising cost of standard fuels.
- End user ~ Once installed the solar system should provide around 50-60% of the annual domestic hot water requirements, in some cases your standard gas boiler would not be required for hot water for some of the summer months.
- Along with the feel good factor of helping the environment, solar systems will of course save you money. This amount will depend on the fuel type you are replacing.
Maintenance ~ These costs are normally very low, most panels will only need to be visually checked yearly, with a more in-depth service every 3-5 years.